The Importance of Quality Assurance
The foundation of any healthy relationship is trust. This is no less true regarding the relationship of the customer and the business. One of the key elements to building this trust is delivering quality products. As far as the Micropulse unit is concerned there are three different sectors of QA testing that are needed to ensure quality. The well-known trinity we call hardware, firmware, and software.
Hardware
Hardware is the physical board, components, chassis etc. Everything physically tangible about the product is referred to as hardware. Imagine buying a brand new TV and it not showing anything but a blank black screen when powered on, or just a black spot in the corner while the rest of the picture was fine. These are examples of Hardware defects/failures that could have been prevented with proper QA. Now an example of a hardware failure with an MWD tool might be accels dying during a job
(Refer to this blogpost for infomation on the importance of the accels)
Dead accels would not be able to give accurate measurements that a job would need. In the example with a TV you can just return it to customer service no problem. This is not the case for an MWD job. These rigs cost a large amount of capital to operate. In short, the stakes for failure are much higher. Luckily, each micropulse goes through a standard and thorough amount of testing throughout its life-cycle before it is shipped.
The first test the micropulse board gets to take is a ring out test. This is an automated test that simply measures the resistance between all the wires on both ends of the tool. This mainly used to ensure that it has been wired properly after the initial manufacturing steps(stay tuned for a more detailed blog to come regarding the ring out testing process).
After the ring out test has been completed the tool is sent to be programmed with firmware that allows us to run scripts that test the functionality of each component on the board. (Mags, flash chips, etc).
After we have insured the quality of the wires and components we then perform a thermal soak. Don’t try this at home with any of your electronics, but we bake micropulse in an oven for several hours(While closely monitoring its readings). The purpose is to test how well the hardware can handle the extreme heat during a job.
If at any point the micropulse board would have a failure it would have been debugged by engineers and restarted the entire process. We repeat this process once more after the tool has been mounted in its chassis as it is prepared for the final test.
I like to think of this test like the final exam needed to pass just before graduation. A lot of guys here like to call it the “Shake n bake” test. Essentially, we take the tool to Dynaqual. We put it in a big chamber that applies rapid heat and cooling cycles while simultaneously applying a large amount of vibration.
Check out the podcast we did our friends from Dynaqual.
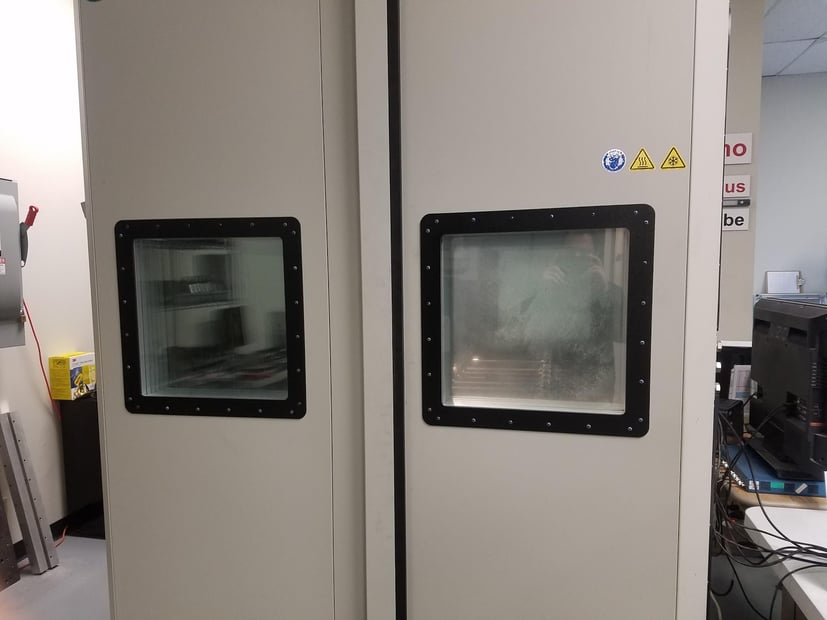
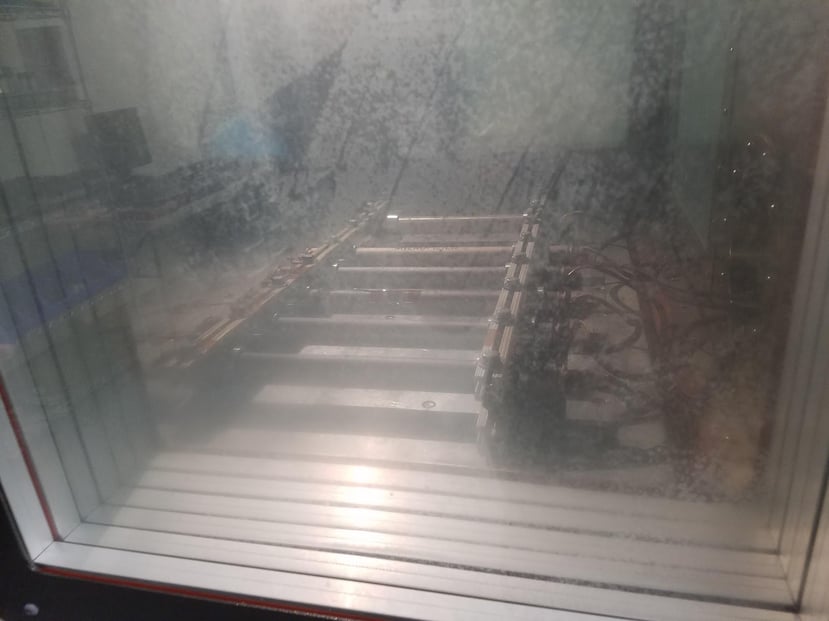
(Pictured is the chamber for the testing)
Typically the environment here is more stressful than what the tool would generally experience in a real-world setting. Even NASA uses these chambers for their stress tests! If it survives this test, then it is ready calibrate and ship!
As far as hardware goes, that is the high-level process.
Software and Firmware testing article to come...